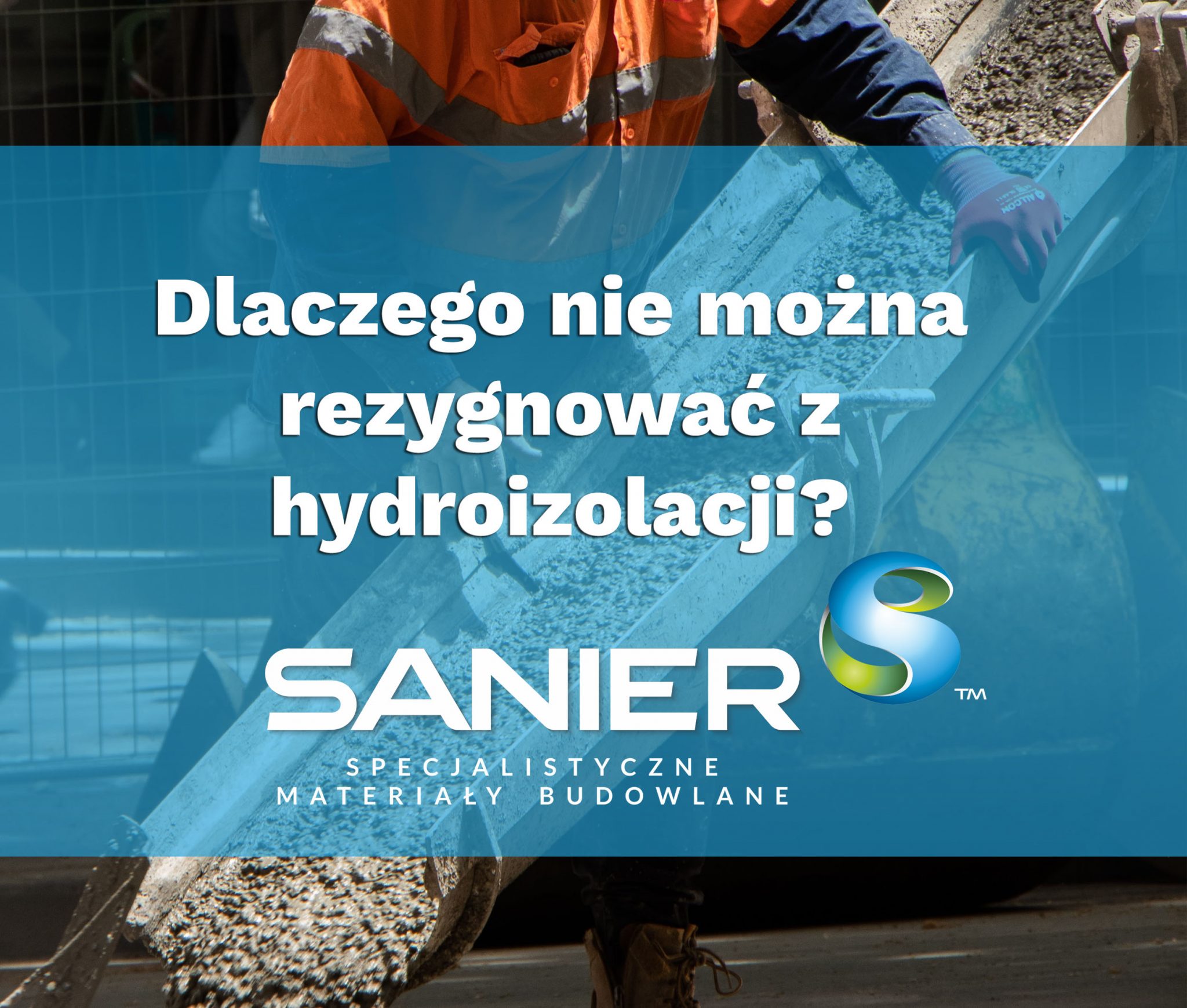
Why You Shouldn't Skip Waterproofing?
August 24, 2022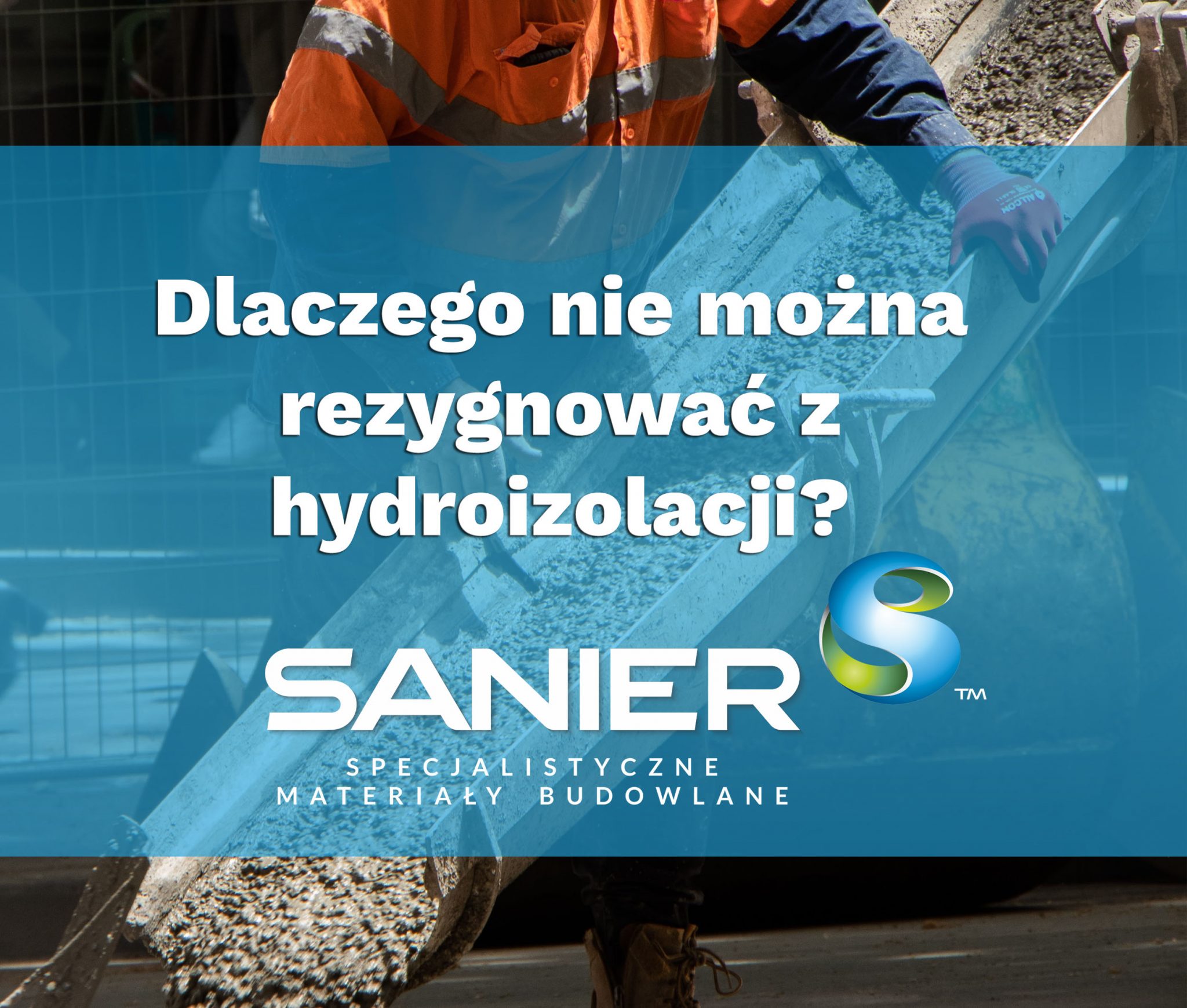
Why Waterproofing Cannot Be Overlooked?
September 2, 2022"White Tank" using the BETOCRETE-C crystallizing admixture
"White Tank" Technology – Why Does It Have a Bad Reputation?
The "White Tank" method is one of the most commonly used waterproofing techniques in Poland, yet it often carries a negative reputation. Why is that?
In Poland, there is no single, clear definition of this concept. The "White Tank" technology was introduced from Germany, and while significant advancements have been made in concrete technology over the years, outdated guidelines are still frequently used.
On the Polish construction market, "White Tank" solutions are primarily developed individually by contracting companies, each following its own approach. The "White Tank" is not a standardized concept, but rather a technological vision offered by suppliers of coating-free waterproofing systems, along with the necessary accessories for sealing construction joints.
What Is the Polish "White Tank"?
The "White Tank" is a coating-free waterproofing system. It consists of a monolithic reinforced concrete structure, typically made in Poland using "waterproof" W8-class concrete.
In this system, concrete serves both as a structural element and as a waterproofing layer. However, the "W" rating in W8 concrete does not mean complete waterproofing—it only indicates a level of water resistance.
For testing standard concrete, the PN-88_B-06250 standard requires six cubic samples (15 cm each). According to the standard, two out of six cubes can fully absorb water, yet the W8 rating is still considered met.
This raises a critical question: is this approach appropriate for designing "White Tank" structures?
Additionally, "White Tank" concrete is poured in stages known as "pours" or "tacts", designed to control planned cracking in designated areas. The maximum allowable crack width is typically 0.2 mm for hydrostatic water pressure, as specified in Eurocode 2.
Why Does the Polish "White Tank" Have a Bad Reputation?
One of the main issues with the "White Tank" method in Poland is the lack of sufficient knowledge among professionals responsible for its design and execution. While this is not always the case, it often leads to the repetition of outdated solutions, ultimately causing problems later in the process.
Most structural engineers focus primarily on the strength class of the concrete, treating "White Tank" structures as just another reinforced concrete element. In practice, they calculate the structural load capacity of the building and, if the foundation is exposed to water, they specify W8 "waterproof" concrete—often without further consideration of waterproofing details.
However, it is essential to understand that W8 concrete is not fully waterproof. Furthermore, the P-NB-06265 standard has removed the "W" rating for water resistance.
This means that modern projects should not specify the "W" rating, as current standards only reference penetration depth under hydrostatic pressure.
A major issue is that construction projects are increasingly being built on challenging terrains, requiring deeper underground levels (-1, -2, and even -3). As a result, buildings are exposed to more complex groundwater conditions and aggressive chemical environments.
Failing to properly specify waterproofing requirements often leads to repeated structural failures—especially in difficult water conditions.
Risks Associated with the "White Tank" System
The "White Tank" is only as waterproof as its weakest element. The first challenge arises during the design phase:
- A separate "White Tank" project is required alongside the main structural design.
- Few designers specialize in "White Tank" systems, limiting expertise.
- Construction companies often create their own versions, instead of following standardized solutions.
If a mistake occurs in the design or execution, even high-quality concrete won't ensure full waterproofing.
Additionally, concrete placement and curing are critical. Key challenges include:
Weather conditions (beyond human control)
Worker discipline (concrete curing is often neglected)
Execution errors (improper reinforcement or misinterpretation of project specifications)
Strict technological discipline is necessary—even small deviations can lead to leaks.
However, an advantage of the "White Tank" is that leaks are easier to locate. If water leaks from a specific joint, it pinpoints the exact problem area.
In contrast, coating-based waterproofing allows water to spread between the membrane and concrete, making leak detection difficult—sometimes, the leak appears far from the actual failure point.
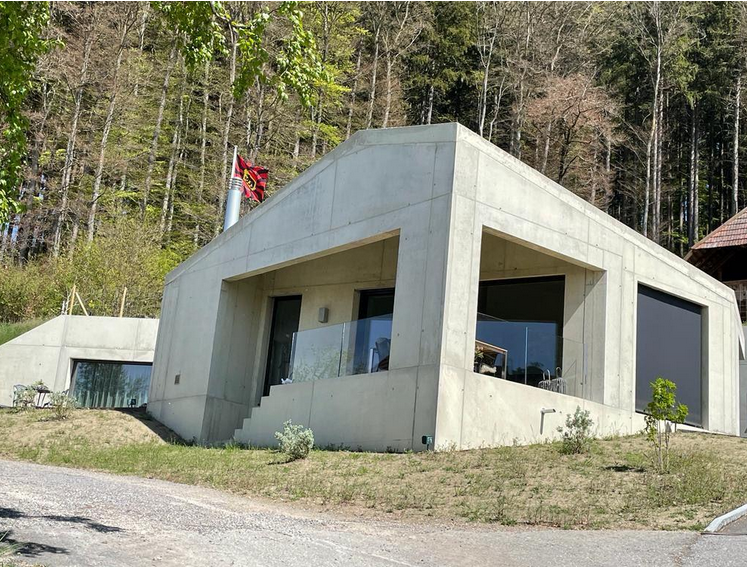
Single-family house in Switzerland using concrete with a crystallization admixture BETOCRETE CP 360 WP.
"White Tank" Technology on a Standard Foundation
Schomburg offers its proven worldwide system of coating-free waterproofing known as the "White Tank", utilizing BETOCRETE-C, a crystallizing admixture that enhances the self-healing of shrinkage cracks in concrete.
The BETOCRETE-C system provides a fully developed set of standards, making design and implementation easier.
In this system, the external part of the foundation is made of water-resistant concrete incorporating BETOCRETE-C, with sealed construction joints at slab-wall, wall-wall, and slab-slab connections.
What Are the Advantages of the BETOCRETE-C System?
Polish regulations allow for the design of structures with cracks up to 0.3 mm wide. In contrast, Schomburg’s BETOCRETE-C concrete mix meets Eurocode standards, which limit the maximum crack width to 0.2 mm.
This difference is crucial for waterproofing.
- A 0.3 mm crack allows water to be absorbed into the structure.
- A 0.2 mm crack prevents water penetration.
This has a direct impact on durability and waterproofing effectiveness. If water enters the structure, it transports harmful substances such as sulfates, CO₂, and chlorides, which corrode reinforcement steel.
As pH levels drop due to water exposure, steel reinforcement depassivates, leading to rapid corrosion, structural degradation, and crumbling of concrete layers.
Eurocode 2 (Concrete Structure Design – Part 3: Silos and Liquid Storage Tanks, p.10) limits the design crack width to 0.2 mm.
Why Is the 0.2 mm Crack Width Critical?
Both Eurocodes and Standard 206 place strong emphasis on durability.
According to Eurocode, the expected service life of a standard residential building is 50 years without human intervention. For engineering structures such as bridges, the minimum design life is 100 years.
The BETOCRETE-C SYSTEM is a specialized admixture that seals the microstructure of concrete, ensuring it meets long-term durability requirements. Schomburg's technology extends the lifespan of buildings by 75%, making it compliant with Eurocode regulations.
How to Calculate the Correct Crack Width?
To determine the appropriate crack width, we calculate the Wkl parameter, which represents the water column height in relation to the wall thickness.
For example:
- If the water column is 4 meters and the wall thickness is 0.3 meters, we divide:
4 ÷ 0.3 = 13.3
Using the Eurocode table, we can determine the correct crack width:
- In this case, it should be 0.15 mm to prevent water penetration.
- If the water column is higher, more reinforcement is required, reducing the crack width to 0.1 mm.
The difference between 0.2 mm and 0.3 mm cracks requires approximately 40% more reinforcement, making this an important economic factor in construction design.
Since there are two types of reinforcement—structural and shrinkage reinforcement—a skilled designer must balance these elements carefully to optimize reinforcement without overdesigning the structure.
How Does Schomburg Address the Issue of Cracks?
To address this issue, Schomburg has developed an admixture that actively repairs cracks in concrete.
- Every building will develop cracks over time, even if they are not visible.
- Cracks as small as 0.1 mm or 0.2 mm can only be detected by wetting the concrete surface.
- However, a 0.3 mm crack can allow water to be forced into the structure up to 3 meters under hydrostatic pressure.
What Is the Core Problem?
This brings us to a critical paradox in concrete design:
- More reinforcement requires smaller aggregate (e.g., 8 mm).
- Smaller aggregate requires more cement paste.
- More cement paste leads to greater shrinkage.
- More shrinkage requires even more reinforcement.
This cycle can continue indefinitely, leading to overdesigned structures.
The optimal approach is to increase the wall thickness instead of continuously adding reinforcement. This is particularly important for "White Tank" structures.
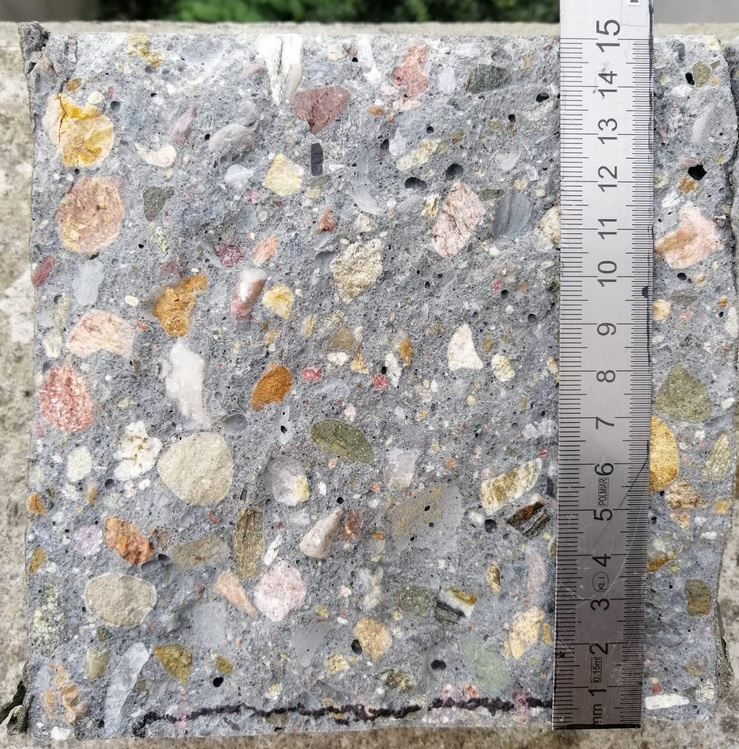
Concrete with an admixture of BETOCRETE-C (maximum penetration depth - 8 mm).
Comparison of W8 Concrete and the BETOCRETE-C System
W8 "waterproof" concrete is not truly waterproof; it is merely tested for water resistance.
- Six cube samples (15 cm × 15 cm) are subjected to water pressure starting at 0.2 MPa, increasing daily by 0.2 MPa, until the W8 classification is reached.
- Two out of six cubes can completely absorb water, yet the requirement is still considered fulfilled.
- This means water can penetrate up to 14 cm and still be within acceptable limits.
For this reason, W8 cannot be considered fully waterproof concrete. It also fails to meet Eurocode durability requirements, as water exposure leads to reinforcement corrosion.
The most harmful scenario for reinforcement is fluctuating water levels, such as those in coastal areas, which can cause severe structural damage.
Unfortunately, many geological surveys and designs are conducted during dry periods, leading to an underestimation of water-related risks. The real problems arise when heavy rains occur or groundwater levels rise in spring, suddenly causing flooded basements.
BETOCRETE-C does not rely on a "waterproof" rating but instead focuses on limiting water penetration depth.
How Does the Chemical Mechanism Work?
The weakest component in concrete is calcium hydroxide, which leaches out easily.
- It diffuses outward, reacts with CO₂, and forms calcium carbonate, appearing as white efflorescence on concrete surfaces.
- Over time, these efflorescence deposits disappear, but the extracted material leaves behind microscopic voids in the concrete.
- This pumice-like porosity is characteristic of W8 concrete, and once water infiltrates these voids, corrosion begins.
The BETOCRETE-C system modifies this process:
- Calcium hydroxide, BETOCRETE-C admixture, ground moisture, and CO₂ interact.
- Insoluble crystalline structures form inside the concrete.
- These crystals permanently seal the structure.
Unlike temporary coatings, BETOCRETE-C remains active throughout the building’s lifespan.
- If cracks form due to structural shifts (e.g., mining subsidence or vibrations), the admixture will self-heal them.
- Even if the building "settles" and a crack appears, the BETOCRETE-C system can permanently seal it.
It takes 7 days to seal a 0.1 mm crack and 21 days to fully repair a 0.3 mm crack using the crystallizing admixture.
Why Do Capillaries Form in Concrete?
A cubic meter of concrete typically contains ~165 liters of water, but only 75 liters are required to hydrate the cement.
- The excess water is necessary to maintain workability during pouring.
- Once the water evaporates, it leaves behind capillary networks.
- These capillaries allow water to infiltrate the structure over time.
To counteract this, Schomburg developed an admixture that crystallizes within capillaries, blocking water ingress and strengthening the concrete.
Since capillaries weaken the structure, their elimination enhances concrete durability and performance.
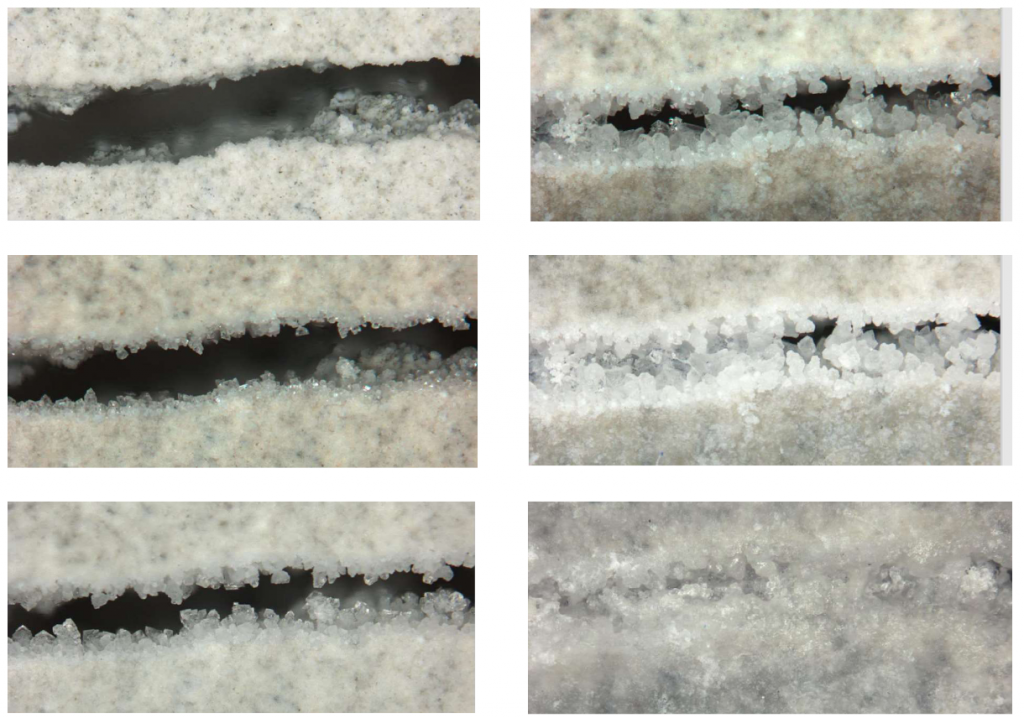
The process of self-healing of shrinkage cracks using BETOCRETE 360 WP.
BETOCRETE-C System
The BETOCRETE-C system is an integrated crystalline waterproofing solution for concrete, acting as a concrete-sealing admixture.
- Through a chemical reaction within the concrete, BETOCRETE-C forms crystals that seal surface cracks up to 0.5 mm and diagonal cracks up to 0.4 mm.
- This system creates a fully impermeable concrete structure, enhancing resistance to water and environmental damage.
- The innovative formula combines crystallization technology with waterproofing agents, extending building lifespan by up to 30 years.
Schomburg has developed four types of admixtures:
- Two liquid formulations (including BETOCRETE-CL210-WP, designed for seawater resistance).
- Two powder formulations (BETOCRETE-CP360-WP for the European market and BETOCRETE-CP350-CI for the Asian market, without the "waterproof" certification).
What Is "White Tank" Technology for Schomburg?
Schomburg’s technology aims to eliminate risks associated with "White Tank" construction.
- The company partners with ready-mix concrete producers, providing technology, admixtures, and expert supervision during mix design.
- The contractor is responsible for developing the construction plan and sealing the structural details.
- Only the combination of all these components results in a fully watertight "White Tank" system.
Want to Learn More?
Detailed information about the waterproofing process can be found in our guide:
Part 1 ← Click to check
Part 2 ← Click to check
Our team of specialists is ready to assist you. If you have any additional questions, feel free to call us at +48 533 343 595.
If you are interested in purchasing materials via sanier.pl and need further assistance, please contact us at: +48 697 691 472 or +48 883 292 303.